Indigenous Material
Clay Aggregates
One of the major factors limiting the development of paved roads in Guyana is the exorbitant cost of stone aggregate and binding materials (such as bitumen). Aggregates are typically mined in the interior of the country, and must be transported at great cost to the coast. Binding materials used on the wear layer of the road surface, such as bitumen, is imported at prohibitive cost, as the country does not yet have a local petrochemical industry.
Compressed Clay Blocks
For centuries, clay and the composites of clay have been a building material of incomparable usefulness and attractiveness. And still today clay has proven itself with excellent properties. From both environmental and economic perspectives, clay is still a valuable, healthy and efficient construction material.
Traditionally, bricks were hand pressed, either sun or kiln dried. Sun-dried earth bricks were produced from the natural sun and air drying process.
IAST developed high compression blocks using coastal clay, these compressed blocks were found to be equal in strength to the concrete blocks currently used in the construction industry at approximately 1/6 of the cost.
Tests and laboratory analyses were done to determine the most appropriate soil for making the compressed clay blocks.
Clay from a predetermined extraction pit was air dried and crushed to smaller particles. The soil was then sieved to remove debris and produce uniformity.
Batches of soil were weighed and the correct proportions of stabilizers, sand and water were added and mixed. Blended into a homogeneous mixture, it was placed into the mechanized block making machine where it was compressed, extruded and placed on the ground to be air dried.
The extruded blocks were stockpiled and covered and cured under a shed for at few weeks and then uncovered and dried for a number of days. The compressed earth blocks were then ready to be used.
The blocks are suitable for the construction of domestic dwellings, since it was tested for compressive strength and compared evenly with cement blocks.
IAST subsequently constructed at 20ft x 20ft Eco-house on the south western of its compound using the compressed earth blocks to build the external and internal walls.
The Environmentally friendly house also has a thatched roof constructed with trouli leaves and windows, doors and furniture made of bamboo materials. The house is power by a solar system.
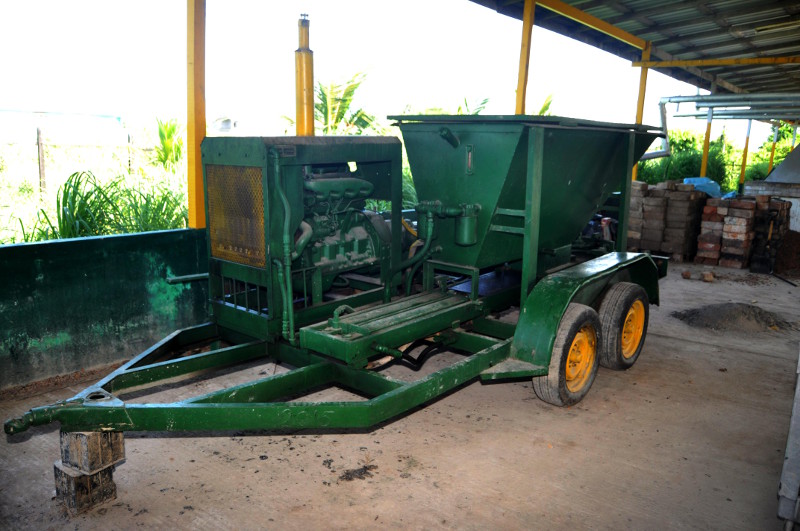
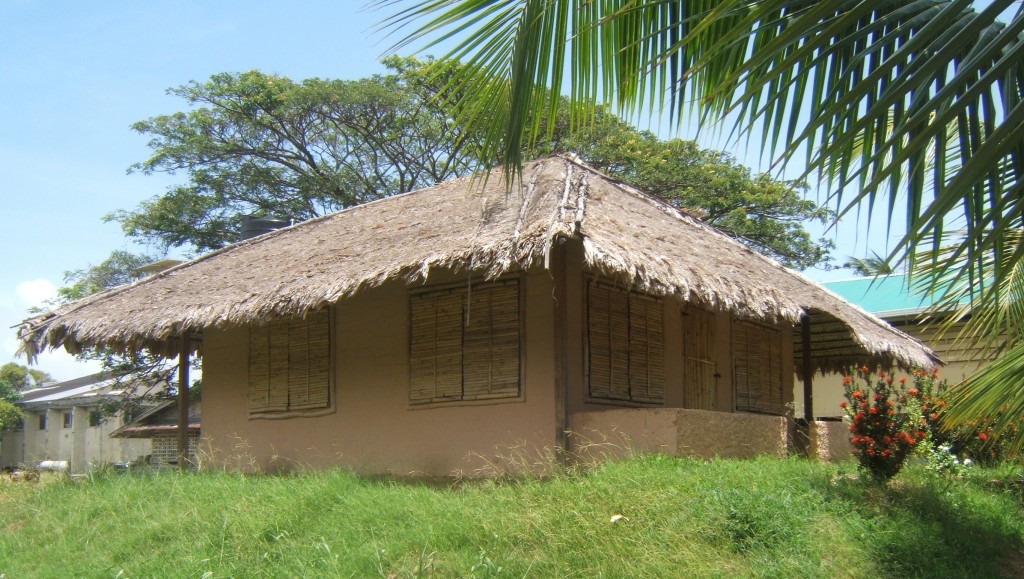

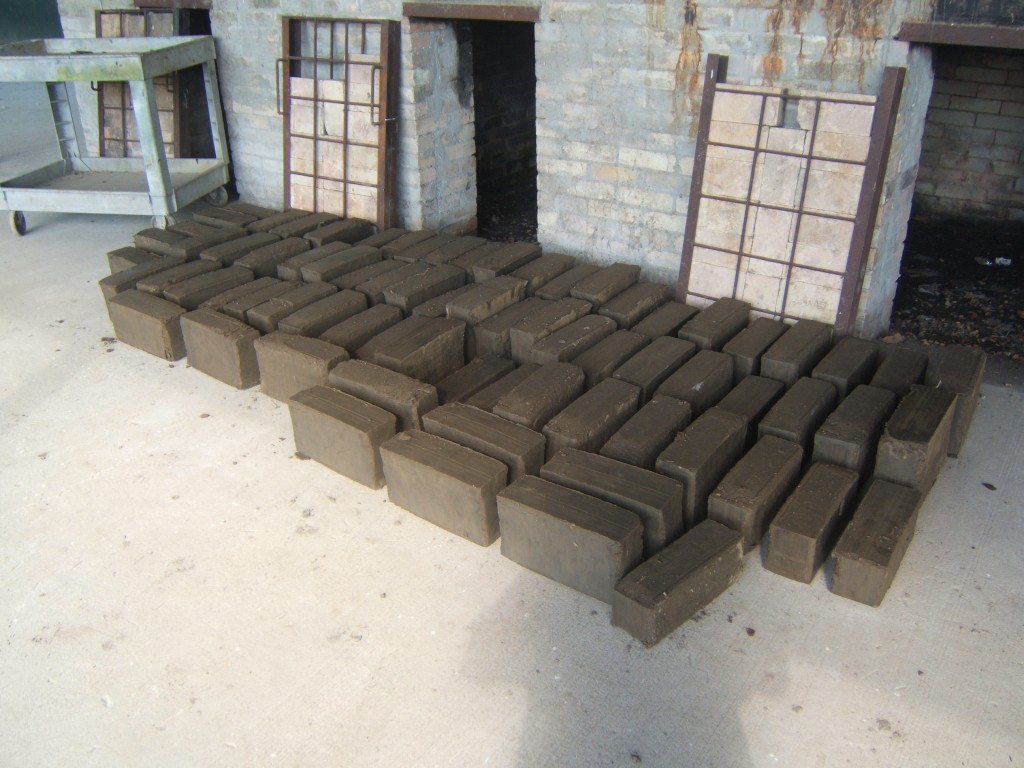
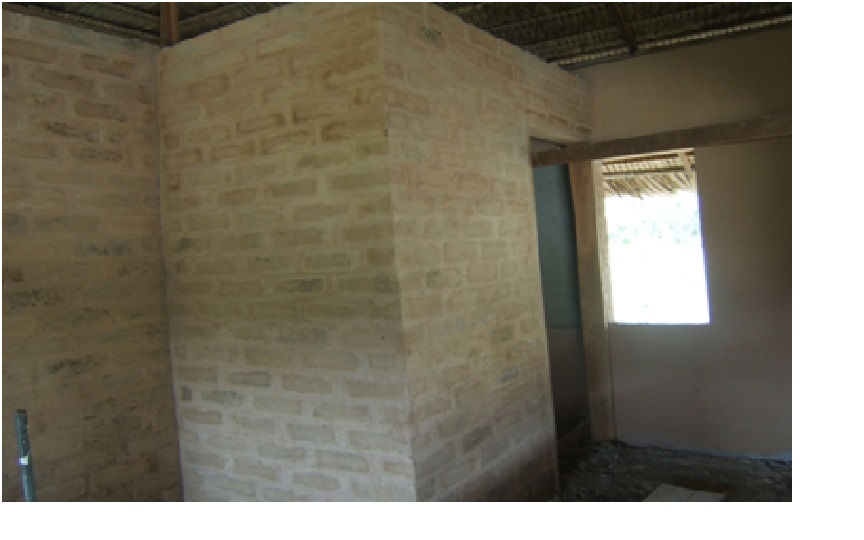
Waste Plastic Composite Building Materials
The Institute of Applied Science and Technology has invested in an extrusion and injection line that produces roof shingles from virgin or recycled plastic resins and waste agricultural fibers.
Plastic composite materials are used in prefabricated, portable, and modular buildings. They can also be used for interior and exterior construction projects such as:
- Exterior cladding and wall panels
- Roofs and Ceilings
- Decks and floor tiles
- Windows and Doors
- Crown mouldings and baseboards
- Bath and shower enclosures and sinks
IAST produces plastic composite materials by thoroughly mixing natural, pulverized agricultural fibers with a thermoplastic resin (waste water bottles, HDPE, etc.) and additives (dyes, chemicals for UV and fire protection).
The mixture is extruded with a parallel twin screw extruder to form a homogenous melt strand that is converted to pellets.
The pelletized material is heated until it is sufficiently fluid to allow for pressure injection into the shingle mold where it solidifies quickly.
IAST estimates a cost of G$280 to manufacture a 16″ (40cm) x 10″ (25cm) plastic composite roofing shingle.
Since 2014, significant effort has expended to engage the private sector in securing an investor to take this project to a commercial scale.
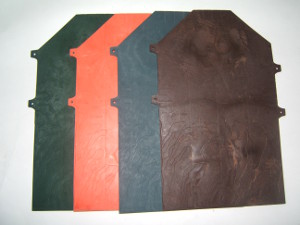
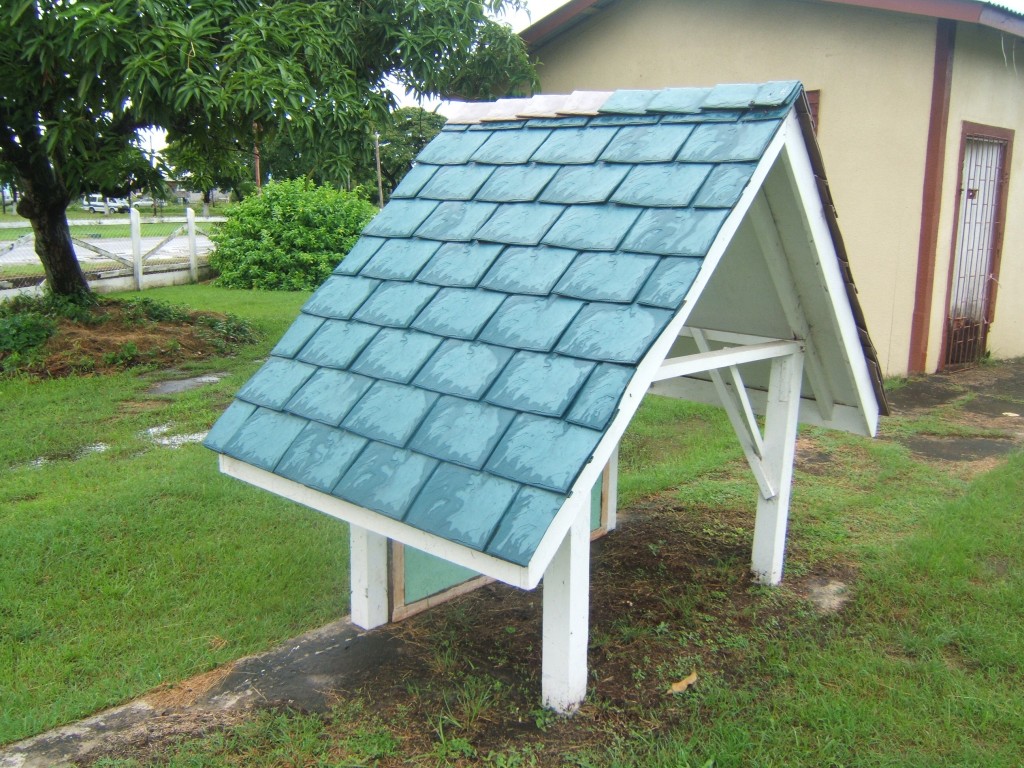
Rubberized Asphalt Cement
The institute has modified and developed technology to reclaim rubber from used tires, and furthermore, to process the recovered rubber particles into rubberized asphalt cement by reacting it with bitumen at high temperatures. The process avoids the use of liquid nitrogen, which is used in other countries, and most of the critical pieces of equipment were manufactured here in Guyana at the institute.
The rubberized asphalt cement was exhaustively tested as a high-friction coating for steel bridges, on the Demerara Harbour Bridge over a period of five years. Bridge engineers reported no failure of the material and superior performance over the imported coating material. The material is also well suited for the repair of highway cracks and for patching cracks and holes due to its high adhesiveness and wide ranges of extensibility, a role for which bitumen alone is ill-suited. In 2014, technical staffs were trained to operate the small mobile asphalt plant and asphalt pump that the institute acquired in 2013 in order to mechanize the operation, increasing production throughput and efficiency. The Institute is waiting on the Demerara Harbour Bridge for approval to commence coating of the entire harbor bridge.
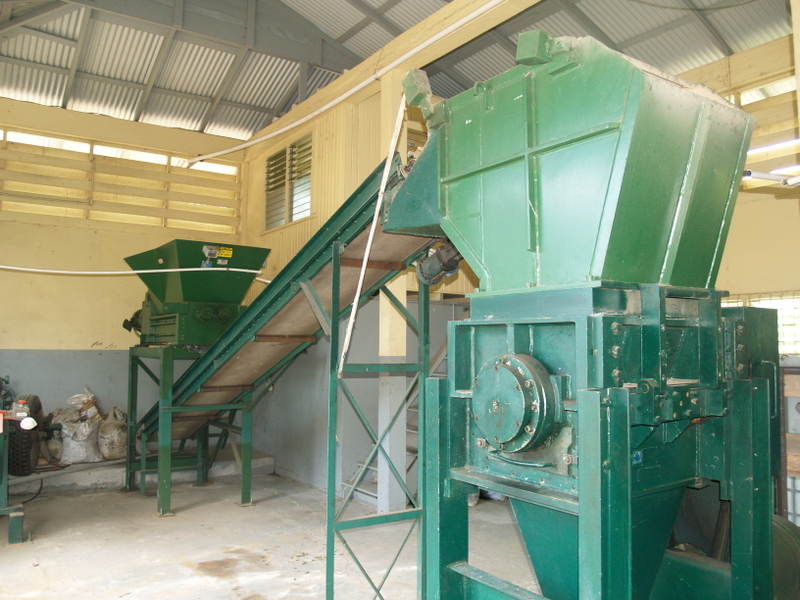
INSTITUTE OF APPLIED SCIENCE AND TECHNOLOGY
UNIVERSITY OF GUYANA CAMPUS,
TURKEYEN, GREATER GEORGETOWN,
GUYANA
TELEPHONE: (592) 222-4212-5, (592)-222-4218, (592)-222-5864
FAX: (592) 222-4229
For further information kindly contact:
Mr. DEONARINE JAGDEO
Director (ag.)
RAYANN HINCKSON
Confidential Secretary
r.hinckson@iast.gov.gy